在全面推进转型发展的关键时期,双钱集团载重公司持续推进节能降耗工作,深化节能意识,创新能源管理,提升降耗技术,推出多项新举措,使节能降耗工作取得阶段性成效。自春节停产检修以来,公司综合能耗显著下降,4月份综合能耗指标在考核线下运行,与去年同期相比有所下降。
以节能理念为导向,深化全员节能意识
通过节能标识的普及,载重公司形成“节约一滴水、节约一张纸、节约一度电”的节能文化宣传氛围,引导全体员工在日常工作、生活中提升节能意识,进一步深化“明目标、定措施、求突破、创佳绩”节能活动。同时结合浴室的用水、用汽的捉漏整改工作,制订《2015年食堂用能标准》,完善外包食堂的用能承包模式,从而有效控制生活及后勤方面的能耗。
在能源管理上突破,完善能源管控网络
载重公司在生产工区设立能源管控小组,将之纳入到能源管理网络当中,提高了工区在能源管理方面的参与度。以压出工区为例,由生产负责人牵头,工区组织管理人员、生产人员组成能源管控小组,与装备能源部维修二区通力协作、联合管理,形成生产工区-职能部门的能源联合管理模式,进行能源管控,通过对预热耗能和各类因素的详细分析,积累数据,找出合理的预热耗能并设定降耗目标;管控小组将能耗控制分解到班组,每日对每班的压缩空气使用量监控,细化到机台和人,通过考核奖励制度的完善进行激励;同时,管控小组对日常蒸汽耗能较大的地点进行以周为周期的检查整改工作,形成管控闭环,加大对现场设备的捉漏、整改力度;利用合理化建议平台,对生产现场“跑、冒、滴、漏”现象检查、整改,落实激励措施,充分调动员工积极性,共同参与到节能降耗工作中。
用降耗技术作支撑,推行节能技术改进
节能降耗工作的有序推进,必须以技术提升作有效支撑,除保温项目等技改措施的投入已产生成效外,载重公司在其他节能技术上也不断加强探索。例如,冷模预热后等待干冰清洗的过程往往会造成一定量预热蒸汽的浪费,技术部门在生产工区的紧密配合下,进行节能试验,完成缩短新车间的冷模预热时间的小批量试验,将热板冷模由目前外温预热6小时缩短为4小时,为降低预热蒸汽的浪费提供了可能;在压缩空气方面,针对实际生产过程中不同的生产规格来调整压缩空气的使用,如:压出工区4#线在生产垫胶时停止使用压缩空气,改用热风机吹干,在生产胎面和三胶角时,通过调压阀调整压缩空气的使用压力,从而节省压缩空气的使用;通过设备上吹风口装置的改进,降低噪音的同时也降低了压缩空气的使用。经过不断的努力,4月份压出工区的压缩空气单耗与第一季度月均单耗相比大为下降。
(责编:Cherry)
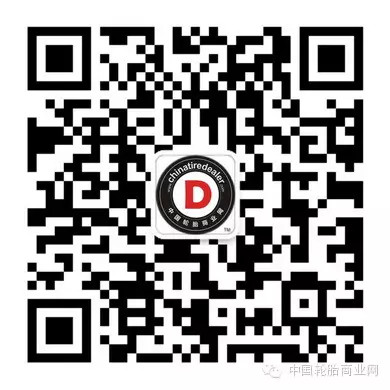